IDoSeaDoo
Well-Known Member
Worked on it quite a bit. Got the sides and bottom cut, bent and mostly welded.
Decided to not cut out the complex shapes of the front and rear walls. Instead I just cut to size a rectangle and welded it on. I'll go back with a router and trim the edges flush before welding the outside. I will need to create a cylinder to recess the fuel pump into the tank so it doesn't stick up and interfere with the low fuel tank ceiling. Also need to cut bend and weld on the troth an the bottom center of the tank and weld in baffles. I'd say on about half way done with this baby!
Sent from my SCH-I545 using Tapatalk
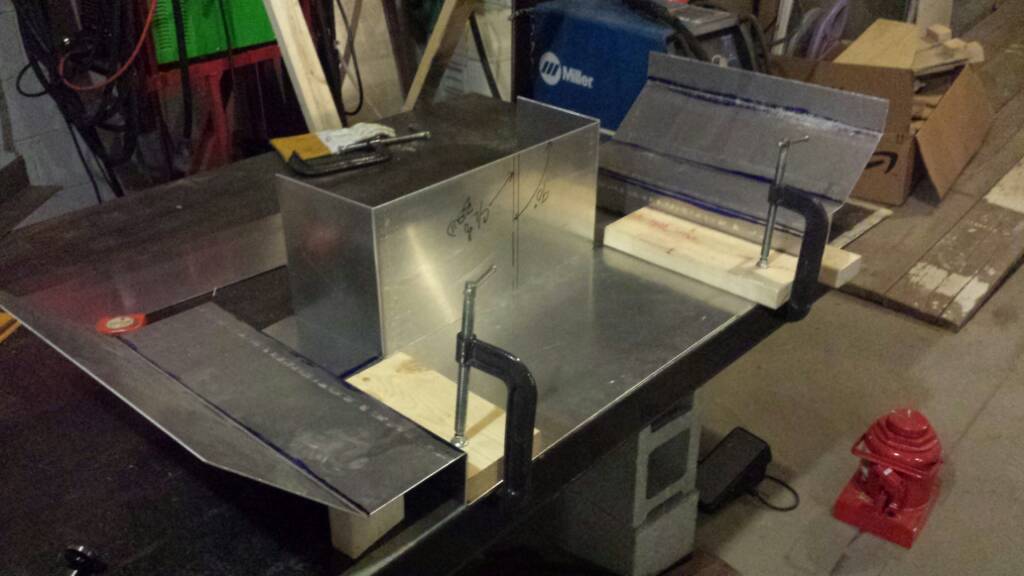
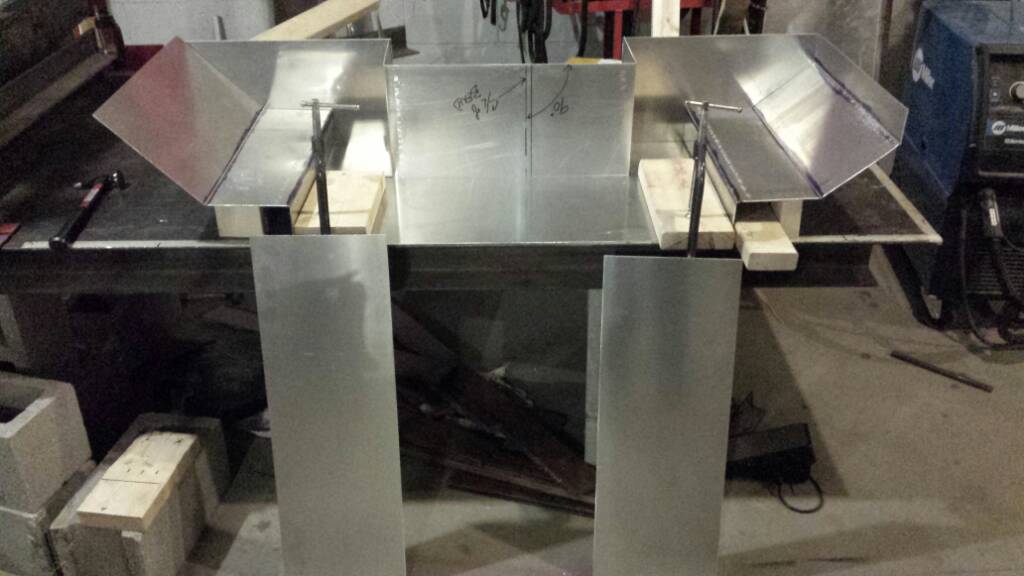
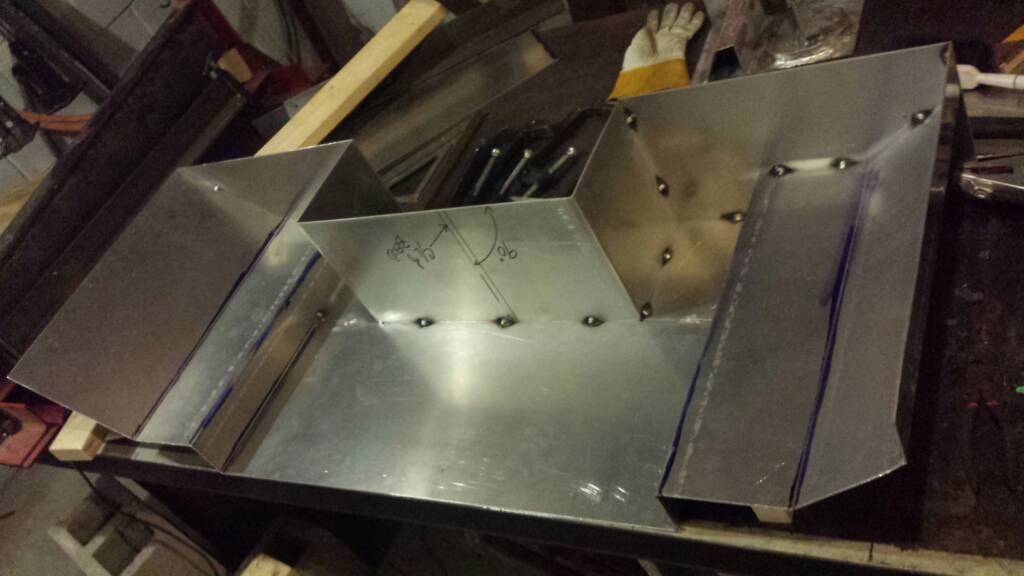
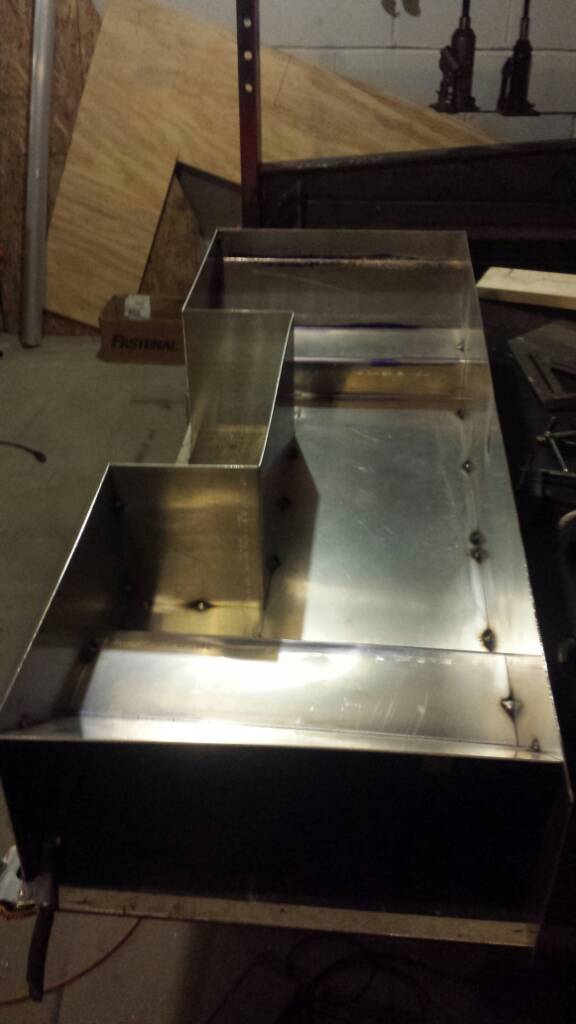
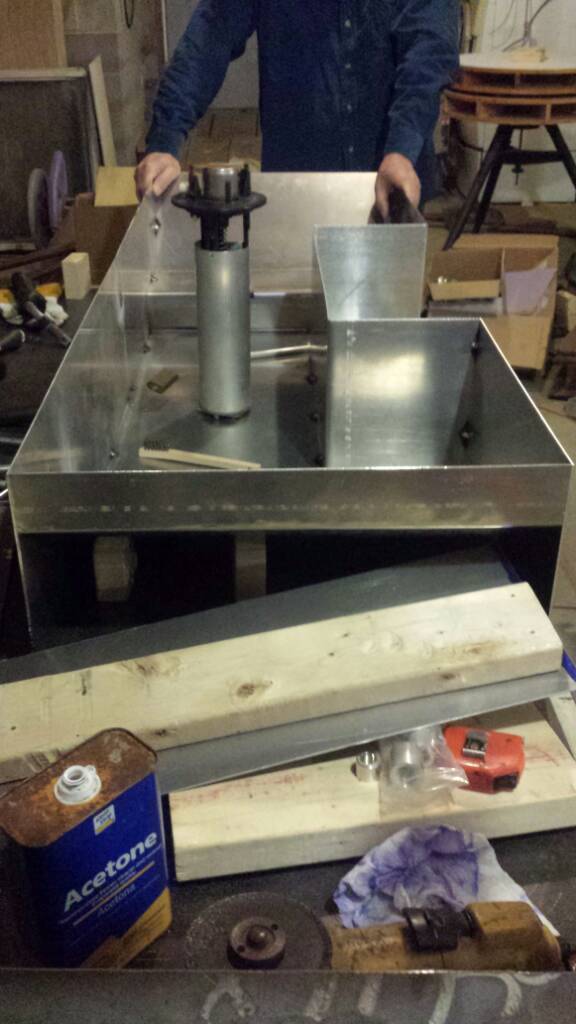
Sent from my SCH-I545 using Tapatalk
Last edited by a moderator: