100guard
New Member
You're awesome. I've started a quick list of things to keep in mind, so I've added your items on it!... Amazon.com
...ultra black RTV (automotive)...
I fill the pump with oil while I have it level on the work bench, just to make it easier looking into the fill plug for oil level...
tighten your pump bolts in a X pattern, hand tighten first to seat the pump in the transom with a new neoprene seal, then torque to proper number...
seadoo synthetic grease on the driveshaft splines and in the impeller splines, don`t fill it , just give it a good coating.
or any good water proof grease will do..
Amazon is good but S&H is brutal unless it's a big purchase to get 'free'. I lucked out and found all the 518 & 592 loctites on Ebay with nominal S&H so I'm waiting on a confirmation. It won't be here for THIS round of rebuild., but next I will be set.
no worries....
100gaurd, sorry for the thread jackl!![]()
is the teflon tape like plumbers tape? I just wrap the screw? Can I similarly use it to wrap the nozzle of my pop-off tester?Use teflon tape on the plug for the cone available at any hardware store--no need for a fancy sealant or even pipe dope from Home Depot or Lowes if you have them north of the border. And if your looking for the 518 to put on the cone--don't bother the o-ring will more than seal it up if it's not messed up. Personally, if you drained the oil and it looked like oil and not like a milkshake your good to go--no leaks. I've had my cones off my 99 every year---still using the same o-ring from 99. Keep it simple.
I am putting up the pics of the oil that came out. Does it look okay? or milkshakey?
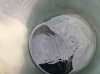
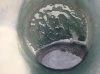
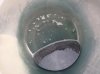
The same oring???? HOLY CRAPPOLA!
I'm new and very wet behind the ears, so I'm gonna over do it just till I get really comfortable. Sealant and everything

Last edited by a moderator: