soccerdad
Well-Known Member
This entire thing was hashed out in another thread. http://www.seadooforum.com/showthread.php?78643-Engine-alignmenet/page2
Since there is a spelling error in the title, and there are several branches in the thread, I decided to post a new clean one.
Using concepts from others, I designed a different way to align a two-stroke, single shaft motor, without having to rent or purchase a SBT tool.
DISCLAIMER- This tool has raised some controversy. I am convinced it is as good or better than the SBT tool. I have heard the SBT tool is really nice, but I have NEVER used one. So, understand the principle, and determine if you want to use it, of course at your own risk.
The concept is simple. The parts do not have to be machined, just cut to length and deburred. And it can be done for around $35. The tool only fits one length drive shaft, so if you have different skis, you may need two or more tools. BUT if you buy 3' of the material (included in the cost), you should have enough material for two different tools! I have a 96 GTX and the leftover material is perfect to use on a 96 XP, GSX and others.
So how does it work? The standard drive shaft has convex splines that allow for some misalignment and flex while you enjoy your ski. This tool replaces the shaft with one that will not move around in the splines. It uses a straight 18mm shaft. The 18mm just fits into the ID of the splined holes in the PTO and prop in the pump. You put a short shaft piece into the PTO, and then put the longer shaft into the splines in the pump. Then you install the pump, tighten it down, and check the alignment. The two shaft ends should be in direct line with each other when it is correct. I also added an 18MM ID sleeve bearing (delrin) to act as a gauge. If you can easily slip the bearing over both shafts, and it turns easily, then you are good to go. The convex shaft allows for approximately 1" of free movement from limit to limit. This tool allows you to align everything as well as practical to make sure nothing binds up while having fun.
So what do you need? You need one 36" piece of 18mm tool steel (drill rod) and one 18mm sleeve bearing. That's it! I got mine from Mcmaster.com Shaft is PN 88625K78 ~$20 and bearing is 2640T23 ~$5. I built a test one out of 3/4 aluminum round bar and just turned the ends down to 0.708" and it worked just as well. So the GTX shaft is 21" long, so I cut the bar 21". Then from that bar I cut a piece 2 3/4" long. Then I deburred them. That is it. You now have your tool. The GSX/XP uses an 18" shaft, so you can use the left over material, along with the 2.75" piece for those skis (and many others).
The high tech tool:
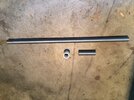
The tool in the pump:
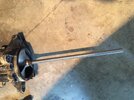
The alignment area- note that you can move the shaft out of the PTO to meet up with the other shaft.
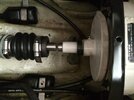
The two with the bearing over them
A final word- The 18mm is very close to the ID of the pump. My PTO easily accepted the tool but the pump was very tight. It seems the prop had a little burr inside from use. I sanded the shaft a little just to polish it up. It start to go on, but I decided not to force it too much. So I grabbed my spare pump and used it. The shaft went in easily, but with virtually no play. So, you may need to use some emery paper or sand paper to decrease the shaft end by .001 or so. Or it may work well. I am sure the material tolerance is in there as well. Or it just may be burrs in my pump.
So, here is a working option, that you can roll your own. It is easy on your wallet and fits in your tool box. And it will work on at least a few different skis. Enjoy. I hope it works well for you.
Since there is a spelling error in the title, and there are several branches in the thread, I decided to post a new clean one.
Using concepts from others, I designed a different way to align a two-stroke, single shaft motor, without having to rent or purchase a SBT tool.
DISCLAIMER- This tool has raised some controversy. I am convinced it is as good or better than the SBT tool. I have heard the SBT tool is really nice, but I have NEVER used one. So, understand the principle, and determine if you want to use it, of course at your own risk.
The concept is simple. The parts do not have to be machined, just cut to length and deburred. And it can be done for around $35. The tool only fits one length drive shaft, so if you have different skis, you may need two or more tools. BUT if you buy 3' of the material (included in the cost), you should have enough material for two different tools! I have a 96 GTX and the leftover material is perfect to use on a 96 XP, GSX and others.
So how does it work? The standard drive shaft has convex splines that allow for some misalignment and flex while you enjoy your ski. This tool replaces the shaft with one that will not move around in the splines. It uses a straight 18mm shaft. The 18mm just fits into the ID of the splined holes in the PTO and prop in the pump. You put a short shaft piece into the PTO, and then put the longer shaft into the splines in the pump. Then you install the pump, tighten it down, and check the alignment. The two shaft ends should be in direct line with each other when it is correct. I also added an 18MM ID sleeve bearing (delrin) to act as a gauge. If you can easily slip the bearing over both shafts, and it turns easily, then you are good to go. The convex shaft allows for approximately 1" of free movement from limit to limit. This tool allows you to align everything as well as practical to make sure nothing binds up while having fun.
So what do you need? You need one 36" piece of 18mm tool steel (drill rod) and one 18mm sleeve bearing. That's it! I got mine from Mcmaster.com Shaft is PN 88625K78 ~$20 and bearing is 2640T23 ~$5. I built a test one out of 3/4 aluminum round bar and just turned the ends down to 0.708" and it worked just as well. So the GTX shaft is 21" long, so I cut the bar 21". Then from that bar I cut a piece 2 3/4" long. Then I deburred them. That is it. You now have your tool. The GSX/XP uses an 18" shaft, so you can use the left over material, along with the 2.75" piece for those skis (and many others).
The high tech tool:
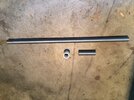
The tool in the pump:
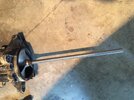
The alignment area- note that you can move the shaft out of the PTO to meet up with the other shaft.
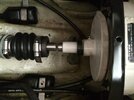
The two with the bearing over them
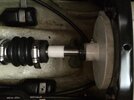
A final word- The 18mm is very close to the ID of the pump. My PTO easily accepted the tool but the pump was very tight. It seems the prop had a little burr inside from use. I sanded the shaft a little just to polish it up. It start to go on, but I decided not to force it too much. So I grabbed my spare pump and used it. The shaft went in easily, but with virtually no play. So, you may need to use some emery paper or sand paper to decrease the shaft end by .001 or so. Or it may work well. I am sure the material tolerance is in there as well. Or it just may be burrs in my pump.
So, here is a working option, that you can roll your own. It is easy on your wallet and fits in your tool box. And it will work on at least a few different skis. Enjoy. I hope it works well for you.
Last edited by a moderator: